本网讯 近日,随着纳雍一厂1号炉最后一台磨煤机油站DCS控制系统调试完成并一次投运成功,纳雍电厂历时三年的一厂1-4号炉磨煤机油站系统性改造工程全面竣工。该项目从控制策略重构、DCS系统搭建到现场调试全程由部门自主完成,不仅实现设备可靠性跃升与降本增效双突破,更培育出一支掌握智能控制核心技术的复合型人才队伍,为企业高质量发展注入创新动能。
破旧立新,从“摸黑运维”到“透明管控”。改造前,1-4号炉磨煤机油站沿用传统PLC控制系统,设备服役超20年,PLC异常、设备跳闸等故障频发。由于PLC程序封闭性强,维修人员无法直观查看控制逻辑,故障排查耗时长,回路设计复杂,严重制约机组可靠性。此次改造中,团队采用分布式控制系统(DCS),将原有PLC控制逻辑采用DCS逻辑控制,就地电接点压力表改成变送器送信号至DCS系统,通过可视化编程界面实现高度可视化监测。运行数据显示,改造后同类故障发生率大幅下降,平均故障恢复时间缩短至20分钟以内,真正实现“故障定位可视化、处理流程标准化”。
淬炼队伍,人才培养与项目攻坚同频共振。该厂以项目为载体,创新“训战结合”培养模式,面对复杂的控制系统升级,以“训战结合”模式培育复合型人才。项目团队将3名技术骨干编入攻关小组,通过“老带新+模块化”培训机制,使全部成员掌握DCS编程与智能诊断技能。在三年改造周期内,累计开展专项培训4场次,培养出熟练进行DCS逻辑组态、画面组态的专业技术人才,能管理项目的专业管理人才。
精益管理,三年谋划铸就精品工程。项目团队科学统筹三年检修周期,早在2022年,该厂便启动“油站改造项目攻坚”行动计划,建立物资储备、技术方案、应急预案储备库,提前储备关键设备,消除因备件短缺导致的工期延误风险。项目团队创新采用“分阶段改造、全流程验证”模式,利用机组C级检修窗口逐台实施改造,同步开展新旧系统并行运行测试,通过边改造、边验证、边优化循序渐进的模式,我们最终如期保质保量的完成了4台机组共16台磨煤机油站控制的改造项目。
目前,改造后的磨煤机油系统已全部稳定运行。此次改造是从“设备维护”向“价值创造”转型的里程碑。此次改造不仅是一次技术升级,更是一场人才淬炼,纳雍电厂将以此次改造为起点,以降本、提质、增效为目标,持续深化自动化技术与生产运维的深度融合,加强运维智能化管理、人才专业化培养,为企业高质量发展贡献更大力量。(通讯员 田红卫 报道)
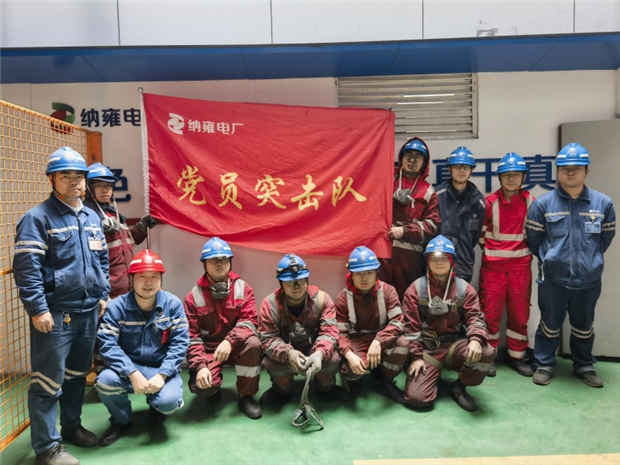